Our artists and product designers create exclusive sketches and 3D renderings based on your requirements. We then move forward to discuss your needs and ideas either in person, by phone or in a joint online meeting. Artistic creativity and craftsmanship are complemented by the most up-to-date CAD and 3D rendering software.
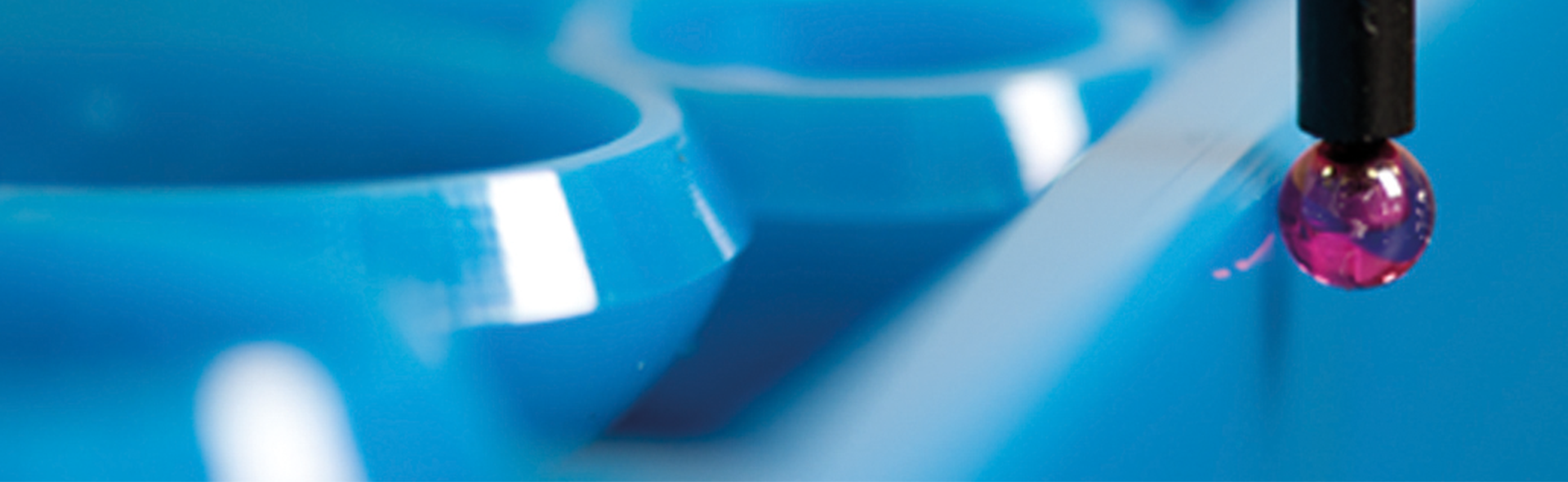
High-precision chocolate moulds for your success
As a traditional company founded in 1935, we are very proud to be one of the world's leading manufacturers of chocolate moulds for pralines, chocolate bars, lollipops and hollow figurines. International confectionery companies, medium-sized chocolatiers and confectioners let us develop their ideas into a wide range of chocolate products. This is always done in close project-oriented cooperation with our customers, as well as with industrial partners, such as plant or packaging machine manufacturers.
Production, that takes place at a single location, guarantees a smooth manufacturing process - from the initial concept to the finished mould. We develop process-oriented solutions for your individual needs using high-quality materials, decades of experience and state-of-the-art manufacturing methods. Continuous quality controls in each work step by our competent and experienced employees ensure an ideal production flow of the moulds. Our approx. 120 specialists, consisting of engineers, artists and for the most part self-trained specialists, form a highly motivated team.
Work flow – Production Process
Our international sales team advises and accompanies you from the initial idea to the final mould.
Design
Product development - single cavity production
First you receive a 3D visualization that enables you to check the design, measurements and volume within an early stage of product development. We can also provide 3D data files or even print 3D models on our own 3D printer and supply them to you.
In case of requested changes, an intensive communication is extremely important in order to meet our customer's requirements perfectly. This can be handled via the usual means of communication as well as directly via online-meetings or personally at our customer's premises with a special software program. Once we receive your approval, our team of experienced toolmakers produce individual polycarbonate samples of the cavity, so that you can test the appearance, weight, surface and demouldability of your chocolate product.
Construction
The next step is the design engineering of the chocolate mould as well as the layout and mould drawing.
Tool manufacturing
Once the product has successfully completed its design and development phase, the process continues with the implementation in tools for mould production. State-of-the-art processing machines and milling centres ensure perfect and repeatable production of the tool components.
Production
Following the tool production, sample moulds are produced for final approval by the customer.
Manual processing and testing complete the partially automatic production on specially equipped injection moulding machines and thermo presses or a combination of both processes.
After approval of the sample mould by the customer, the mould set is being manufactured.
Extras
During production, the moulds can be equipped with additional components such as RFID chips, laser markings, QR codes, codings, detectable material, centerings, hinges, magnets, clips, clamps etc.
Quality Control
Our high quality standards are strictly monitored - at any time, at every stage of production by measurement robots, exercise tests and by every employee.
Tested Quality
We set the highest quality standards for our products. Quality means safety and safety has priority in our actions. The high quality standards are strictly monitored by us - at any time, at every stage of production and by every employee.
The customer always remains the centre of our attention. That is why it is of the highest priority for us to ensure long-term reliable processes for our customers by supplying high-precision moulds, e.g. guaranteeing narrowest tolerances moulds for cold stamping processes.
In addition to TÜV certification according to DIN EN ISO 9001:2015, all moulds are developed and designed in-house and manufactured from food-safe and high-quality plastic materials.
